which are very pronounced in the final test of stretchability of foot and welt. The fit of the foot has a distinct ruling on the fit of the ankle, and as regards the welt this too must accommodate itself to legs which are larger than the average in the area above the knee. In silk, the stretch variance between the rough and the dyed article is very
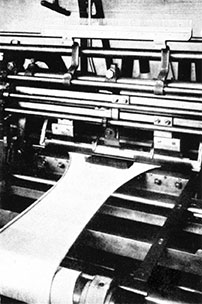
single unit machine.
marked, this being nearly 30% higher in the foot after dyeing (and, therefore, degumming) than when in its unfinished state. In contrast with this, when lisle cotton is used in the welt of a hose, its stretching property is approximately 30% less after finishing than when in its rough state. As regards nylon, its stretch adjustment is approximately 5% more in both foot and welt after dyeing than it is in its after pre-boarding state. An improved method for the greater promotion of stretch in hose made from nylon is the employing of a transitory yarn (a cellulose acetate thread) along with the nylon, both threads (which can be either plated or twisted) being knitted along together. The stocking is then permanently set, and the transitory yarn